what is Milling?
“Milling” is the most common machining method worldwide. Milling is a chip removal process that uses mechanical operations to remove excess material, creating various features on a raw workpiece. This process requires a milling machine, a raw workpiece, a workpiece holding fixture (milling machine clamp), and cutting tools (mill, cutting diamond, etc.). The workpiece, already produced by one of the mass production methods, is fixed on the milling machine table using a clamp. The cutting tool, directly (mill) or indirectly (diamond and milling holder) attached to the spindle’s rotating axis, performs chip removal at a controlled rotational speed and reciprocating movements to eventually achieve the desired shape, usually according to 3D models or engineering drawings.
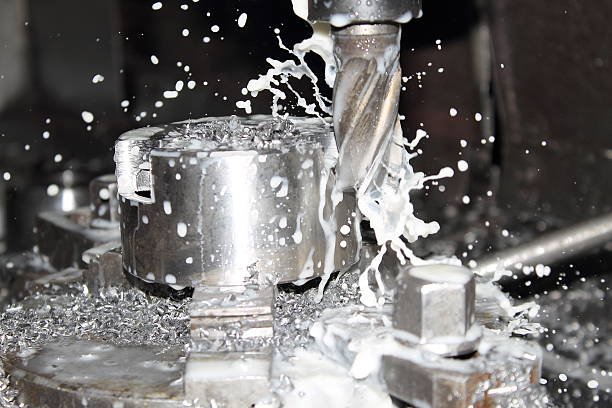
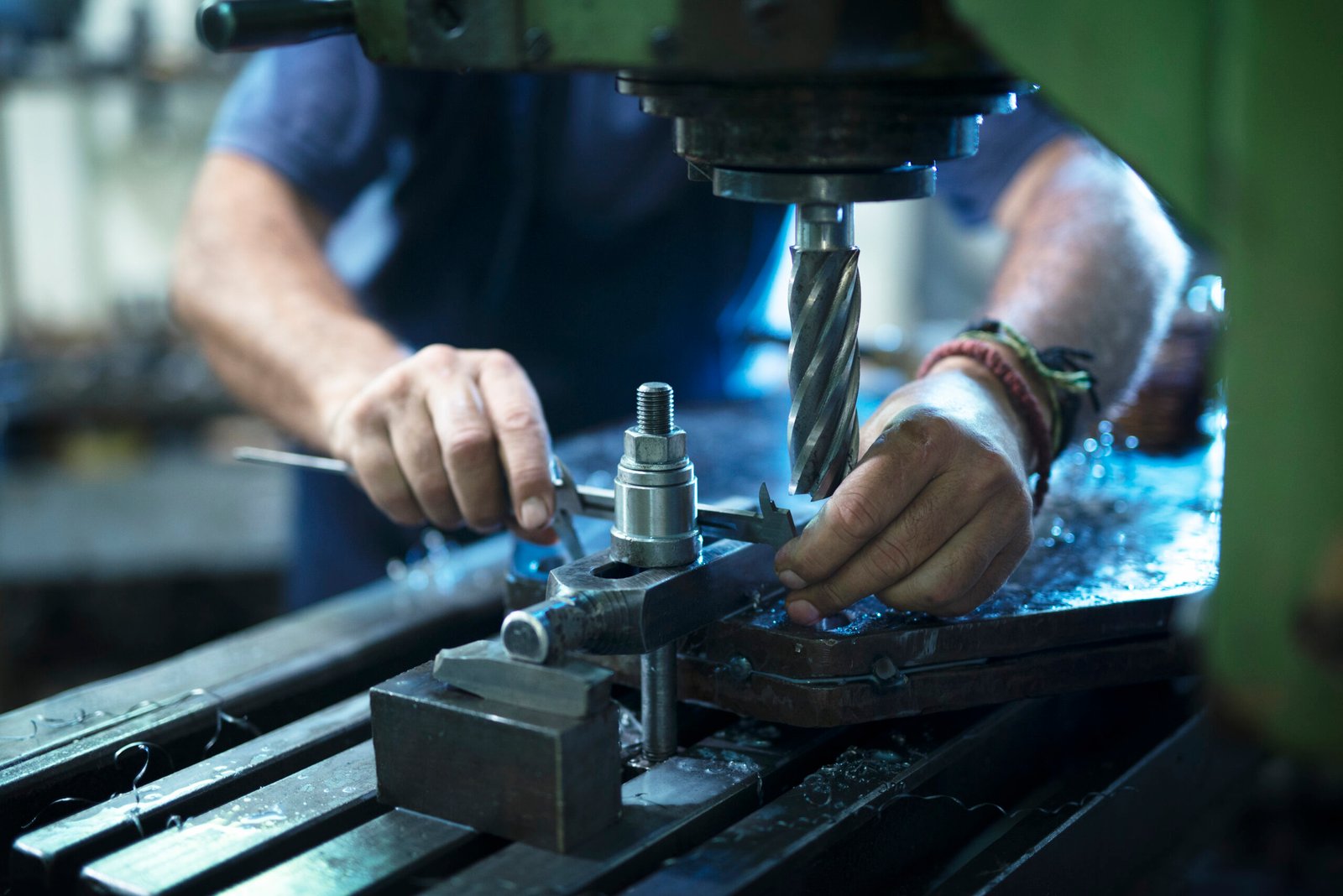
Milling is primarily used for parts lacking axial symmetry and featuring various characteristics like holes, grooves, pockets, and even 3D surface curves (Organic Shape). Parts with axial symmetry are often produced by turning, which is described elsewhere. Parts completely produced by milling are usually limited in number and used for prototyping or producing small industrial assemblies. Another application of milling is producing tools and equipment for other manufacturing processes. For example, 3D molds (bending, deep drawing, plastic injection, etc.) are usually made by milling. Milling is also used in secondary and finishing processes to add special features to parts produced by other methods (like casting), ideal for adding precise features due to its high accuracy and excellent surface finish.
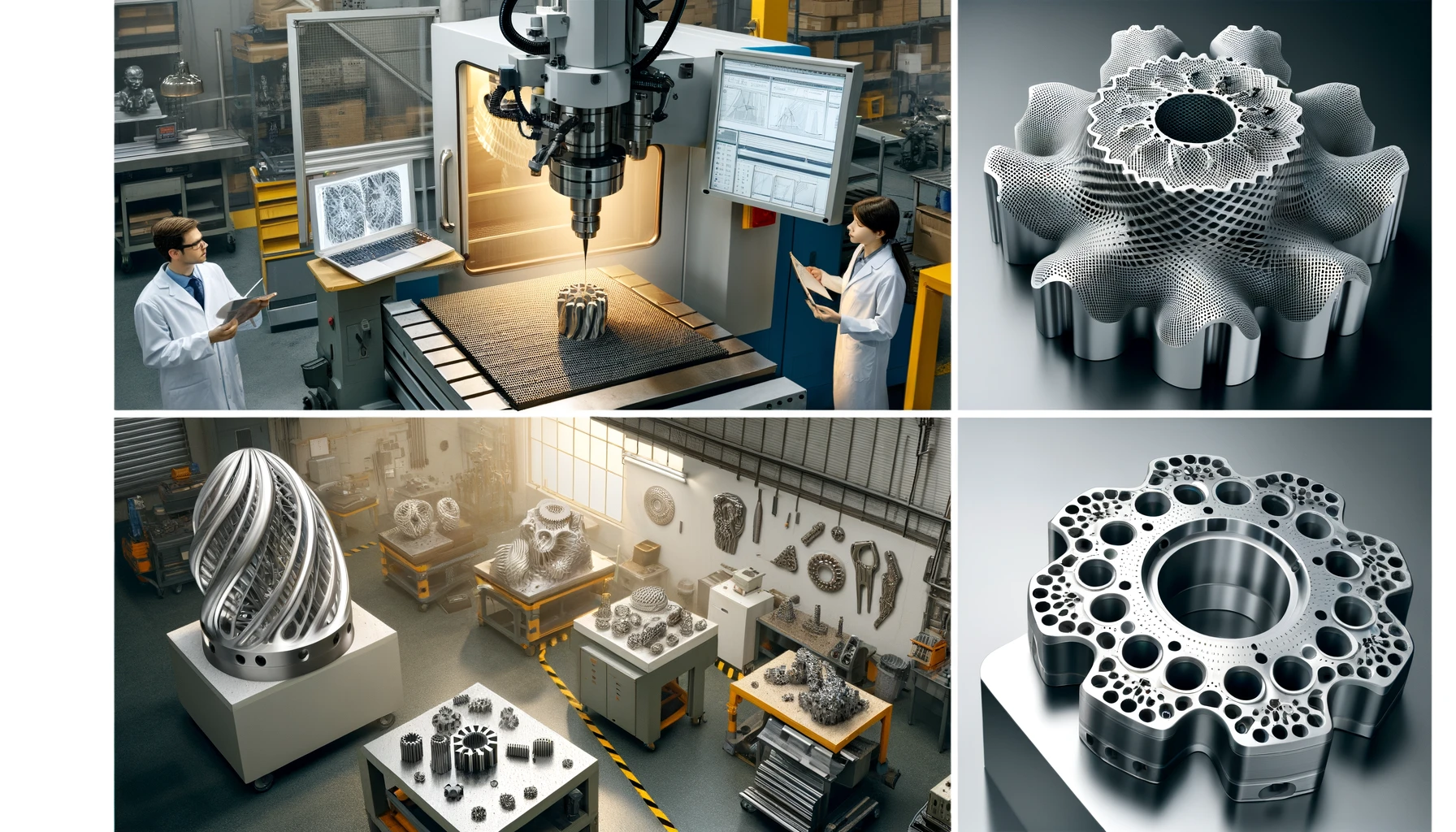
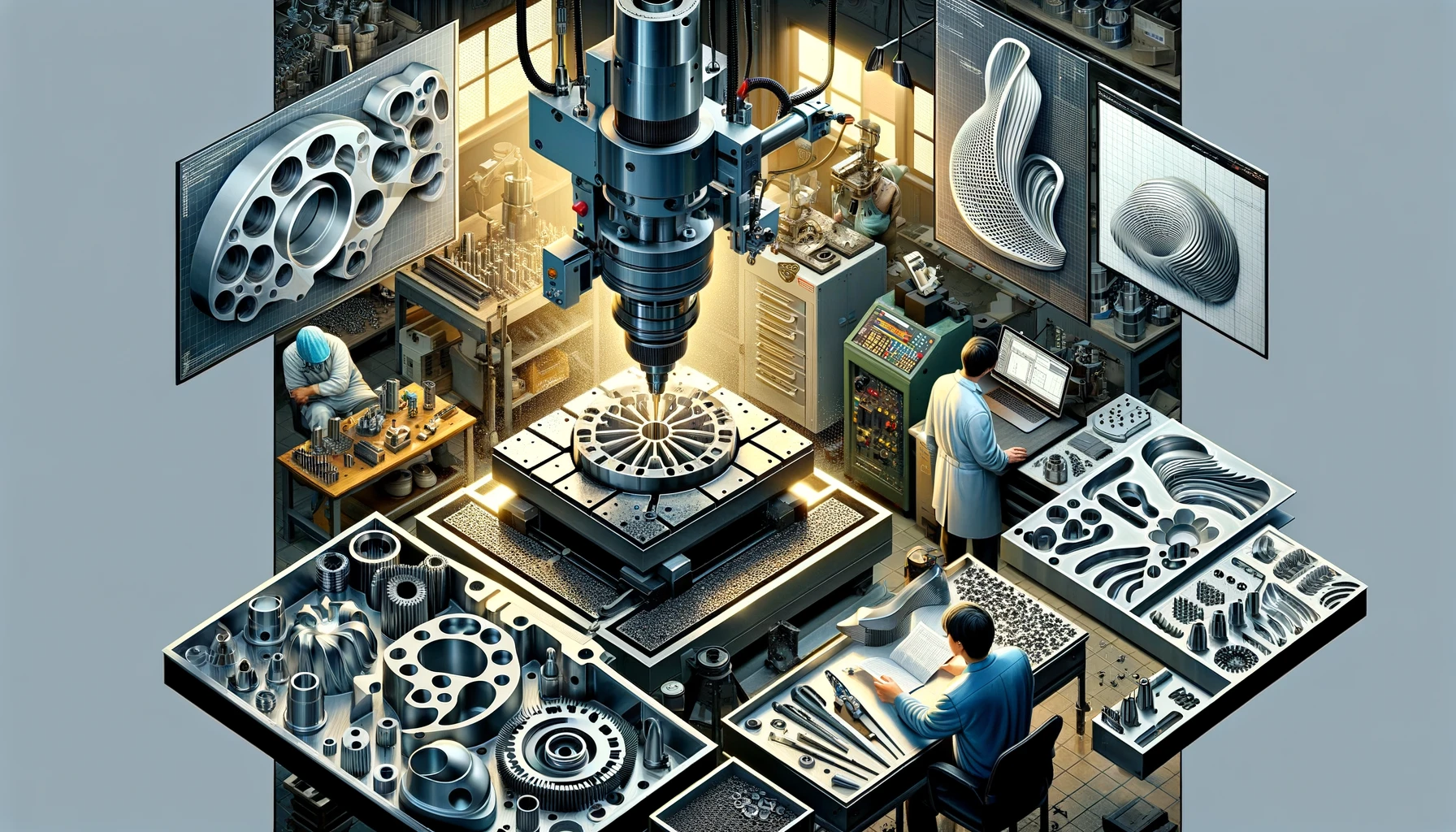
Materials that can be machined by milling include:
- Carbon steels
- Alloy steels
- Stainless steel
- Cast iron
- Magnesium
- Zinc
- Ceramics
- Composites
- Zinc
- Nickel
- Titanium
- Elastomer
- Thermoplastics and thermosets
Important factors in the machining process include the cutting feed, cutting speed, spindle speed, feed rate, and axial depth of cut, all of which are influenced by various factors like the material of the workpiece and the tool, tool size, etc.
Common milling tools and process
Manual milling is a machining process where an operator uses a milling machine to manually control the cutting of material. This process requires a skilled operator to manipulate the machine’s controls, such as handwheels and levers, to guide the cutting tool and shape the workpiece. Manual milling is often used for one-off projects, prototypes, and small batch production, offering flexibility and adaptability for custom designs. While it lacks the precision and speed of CNC milling, it remains valuable for applications where the complexities and costs of CNC programming are not justified. Manual milling is also a key educational tool, helping students and apprentices learn fundamental machining principles and develop hands-on skills in material shaping.
CNC milling is a precise and automated machining process used to remove material from a workpiece using computer-controlled milling machines. In CNC (Computer Numerical Control) milling, detailed instructions are programmed into a computer to guide the cutting tools in creating complex shapes, holes, and features with high precision. This method allows for the production of intricate and complex parts with tight tolerances, which would be difficult or impossible to achieve with manual milling. The key advantage of CNC milling is its ability to produce consistent and high-quality parts at high speeds, making it ideal for mass production and complex designs. The technology is widely used in various industries, including aerospace, automotive, and medical device manufacturing. CNC milling machines can operate on multiple axes (typically 3-axis or 5-axis), enabling them to create parts with intricate geometries and detailed contours. This level of automation reduces the need for manual intervention, leading to increased efficiency, reduced errors, and consistent output quality.
End milling is a versatile milling process that uses a cutting tool called an end mill for material removal. End mills can cut in all directions, making them suitable for a variety of operations like slot milling, profiling, and plunging. This process is widely used in manufacturing to create complex shapes, precise slots, and detailed profiles in workpieces. End mills come in various shapes and sizes, allowing for a broad range of applications across different materials, from metals to plastics.
Chamfer milling is a process that creates bevels or angled cuts on the edges of a workpiece. This technique is often used to remove sharp edges for safety, aesthetic, or part assembly purposes. Chamfer mills are specifically designed for this task, ensuring a consistent and precise angle along the edge. This process is crucial in manufacturing for preparing parts that require angled surfaces for welding, creating decorative profiles, or ensuring a proper fit in assembly.
Face milling is a machining process that involves removing material from the surface of a workpiece to create a flat, smooth surface. This is achieved using a face mill, a cutting tool with multiple cutting edges that rotate around the periphery of the tool. Face milling is ideal for achieving high-quality finishes and is commonly used for machining large areas quickly. It is widely used in the automotive, aerospace, and mold-making industries.
These tools and methods define the versatility and precision of the milling process in modern manufacturing.
Latest Articles in your inbox
Subscribe to our newsletter to get the newest manufacturing and industrial services articles in your inbox once a week.