what is Turning?
Turning, also known as lathing, is a machining process involving the shaping of materials by removing chips with the use of a dedicated turning machine through rotation. In this process, the targeted piece rotates with specific force and speed, and the turning blades move across it to perform chip removal at a determined depth. This definition is applicable to metals, wood, plastics, and many other materials that can be turned and chipped. Turning is one of the most comprehensive methods of manufacturing and producing engineering parts and falls under the category of subtractive manufacturing. This implies starting with a block or cylinder on the machine and gradually chipping away to create the final product.
Turning is commonly used to create parts with axial symmetry, resulting from the rotation of the piece around a specific axis. The process is conducted using lathes and various chip removal tools (like diamond, drill, broach, milling cutters, etc.). Similar to other general manufacturing methods, lathes are divided into manual and automatic (CNC) categories. Initially, manual machines were used in this field, but with the rise of computers in manufacturing and the automation of processes, CNC lathes have also been actively involved for about the past 50 years. An important aspect of turning in part manufacturing is the necessity of using parts with axial symmetry in mechanisms with rotating components. Since the output from the turning process typically has axial symmetry, using these parts as rotating components in an assembly helps achieve dynamic balance.
Various materials, including different engineering metal alloys (steel, cast iron, stainless steel, aluminum, brass, bronze, etc.), engineering polymers, and a wide range of wooden products can be shaped through turning.
The turning process involves several operations, including face turning, outer turning, boring (internal turning), end facing, threading, tapping, screw cutting, taper turning, groove turning, and more. Mastering each of these techniques requires considerable time and effort.
Different Types of Turning Processes?
Lathes are categorized into two main types: manual lathes and CNC lathes. The primary difference between a CNC lathe and a manual one is the programmability of the CNC (via the machine’s panel or computer software) using machine control codes (G-Code). Certain lathes are also customized for specific parts or processes. An example is the crankshaft turning machine.
A general lathe consists of various components like an electric motor (for the power needed in turning), a gearbox (for adjusting the rotational speed of the workpiece according to the turning process), a workpiece holder (three or four-jaw chuck), tailstock, electric box, upper support, machine table, coolant pump and circulation system, speed and movement levers, etc. CNC lathes, in addition to these components, have a control unit (central computer).
Different metallic, polymeric, and wooden materials can be machined and manufactured using a lathe.
Prominent turning methods include manual machine turning, CNC machine turning, portal lathe turning (for very large parts), automatic screw machine turning, and other miscellaneous machines.
Manual Machine Turning:
A manual machine is one that is controlled manually. Manual lathes can be used to create various cylindrical parts with straight, stepped, or angled designs. Various types of holes, threading, and internal turning can also be performed with these machines.
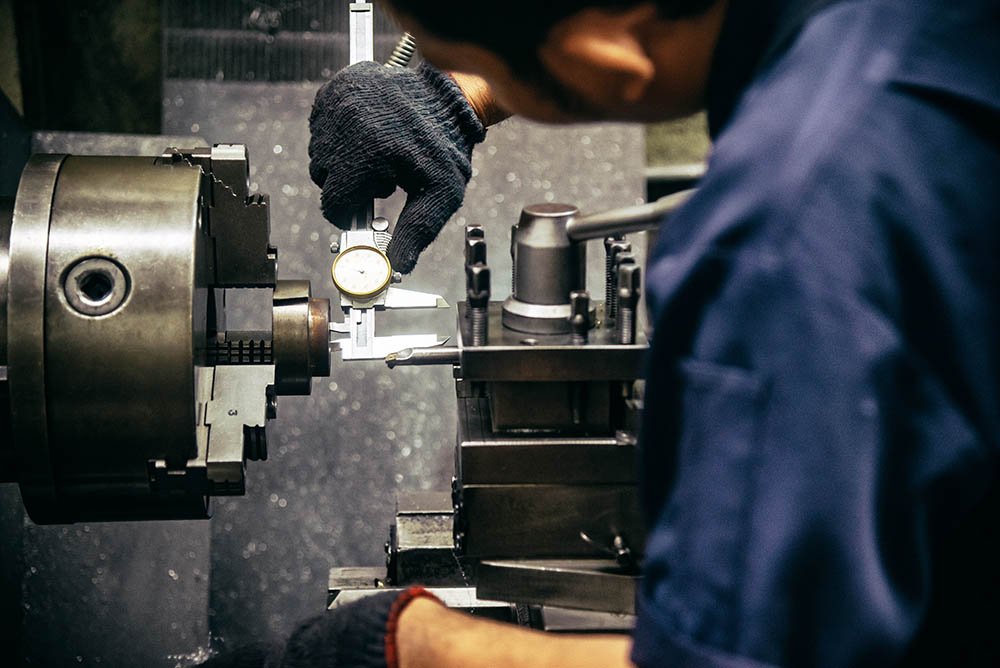
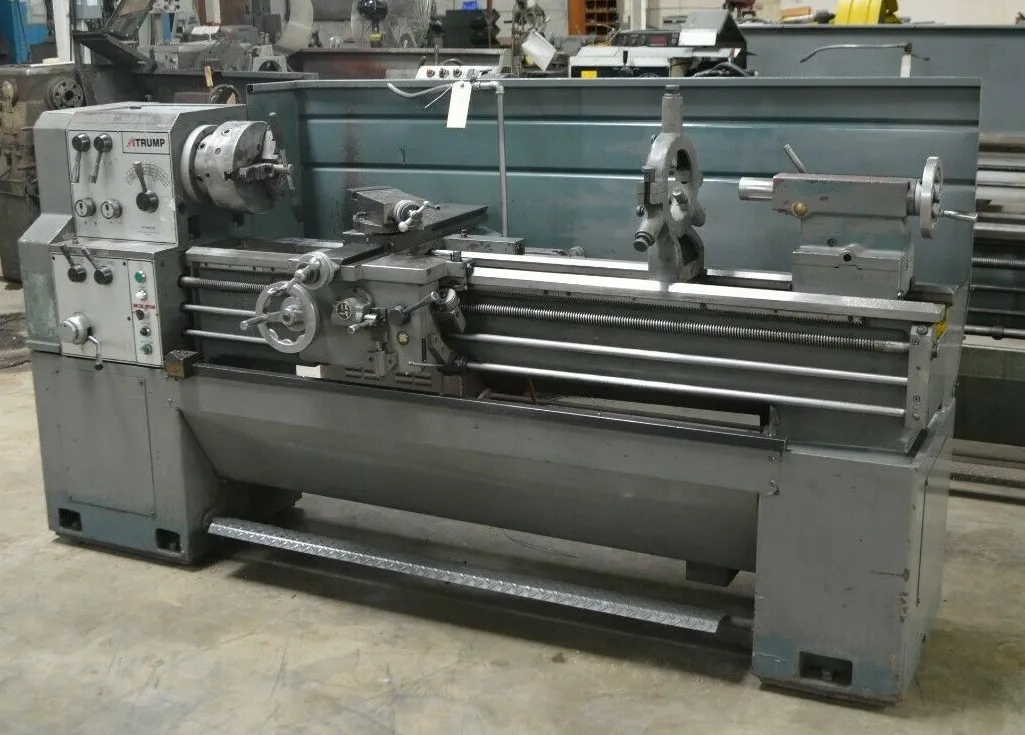
CNC Machine Turning:
CNC manufacturing methods are typically used for complex parts where the desired profile of the piece or the precision required in the process cannot be achieved by a manual lathe operator. This method is fully computer-controlled, minimizing human errors during manufacturing.
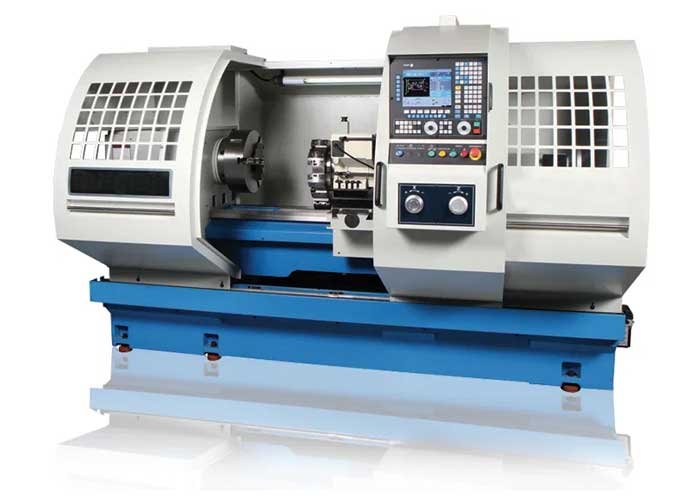
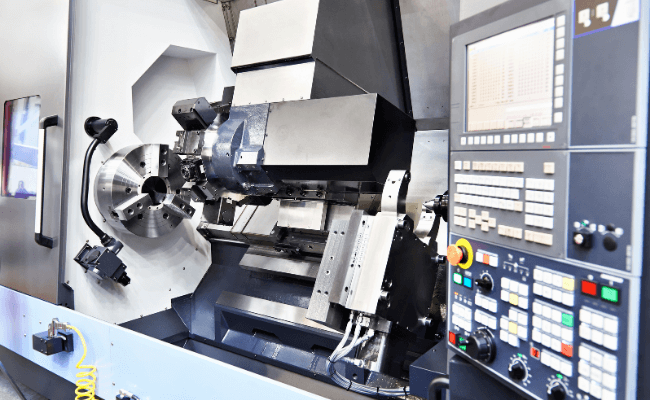
Latest Articles in your inbox
Subscribe to our newsletter to get the newest manufacturing and industrial services articles in your inbox once a week.